Enterprise Manufacturing Intel (EMI)
The need for Modern EMI as the first step in the Journey toward Industry 4.0
The need for Modern EMI as the first step in the Journey toward Industry 4.0
ThinkIQ equips manufacturers to go beyond the limitations of traditional EMI in their transformational journey toward achieving Industry 4.0 Smart Manufacturing.
As the pace of business accelerates, there is a greater need for companies to see and understand manufacturing activity across the extended supply chain in order to make faster, more informed decisions. However complex supply chains, non-standard and distributed operations, and data captured in different formats can make gaining access to such critical operational intelligence difficult.
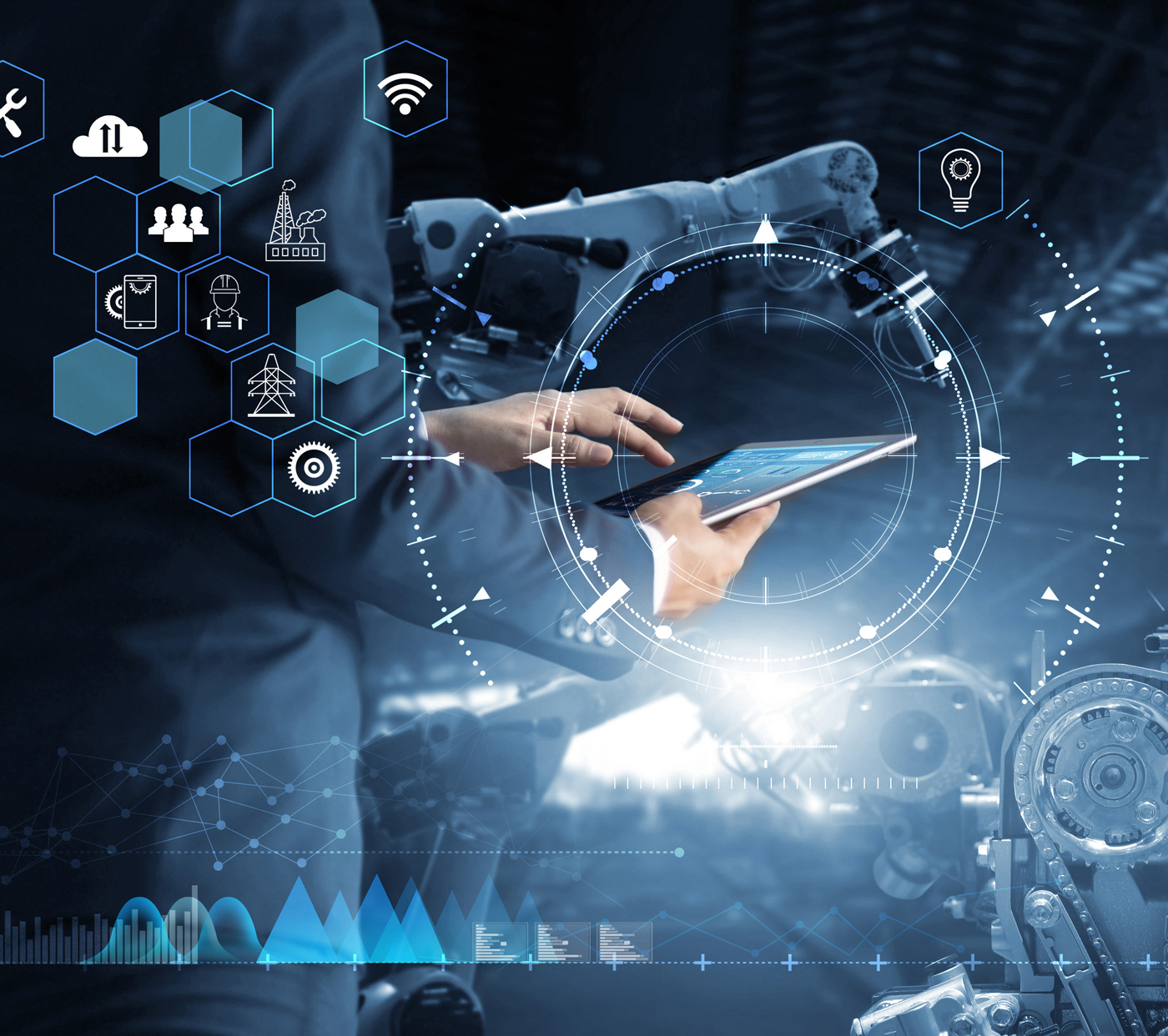

How an Industry Leader in Frozen Food Manufacturing used IoT, Big Data, and Machine Learning to Increase Yield.
Download the Case Study now and see how the ThinkIQ systems can help to expand your business!
So, What is Traditional EMI?
Enterprise Manufacturing Intelligence (EMI) refers to software systems that integrate different sources of operational data for the purpose of deeper analytics, reporting, visual summaries, and the sharing of data between enterprise-level and plant-floor systems. EMI software has become a crucial tool organizations use to gain immediate, actionable intelligence from both shop floor automation and enterprise business systems.
Furthermore, while some may equate EMI with Business Intelligence (BI), there is a difference. BI traditionally measures sales, revenues, and other Key Performance Indicators (KPIs) that are of a corporate nature. EMI, on the other hand, measures the productivity of both the humans and the machines on your factory floor. EMI can plug into BI to add more value to the enterprise, but, by itself, it can still be used as an independent stream of insight into manufacturing operations.
ThinkIQ Visualize™ delivers a revolutionary shift from traditional EMI solutions – as a cloud-native, platform-agnostic solution that can be implemented in manageable increments offering significant benefits at each step in the journey toward Smart Manufacturing.
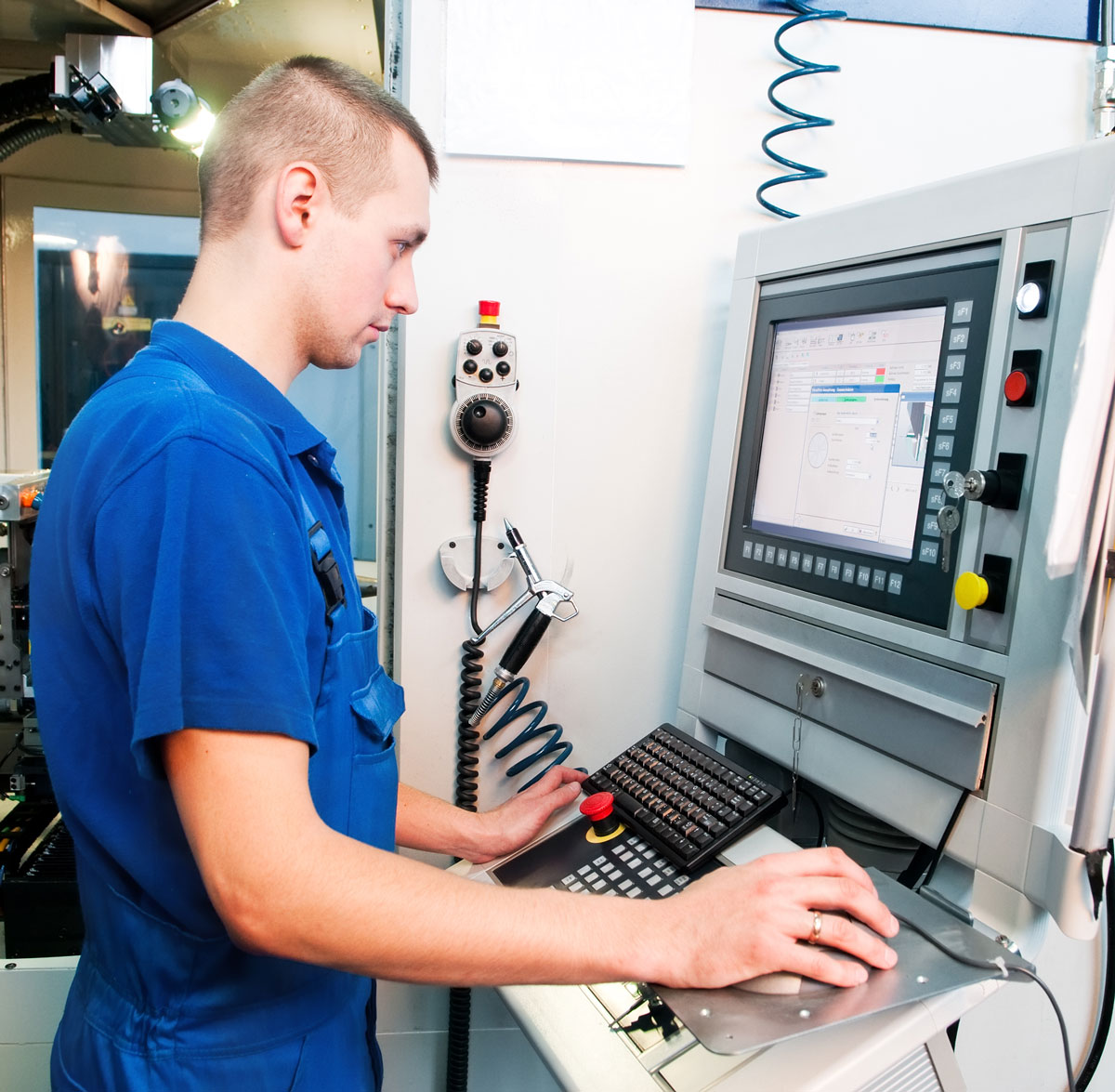
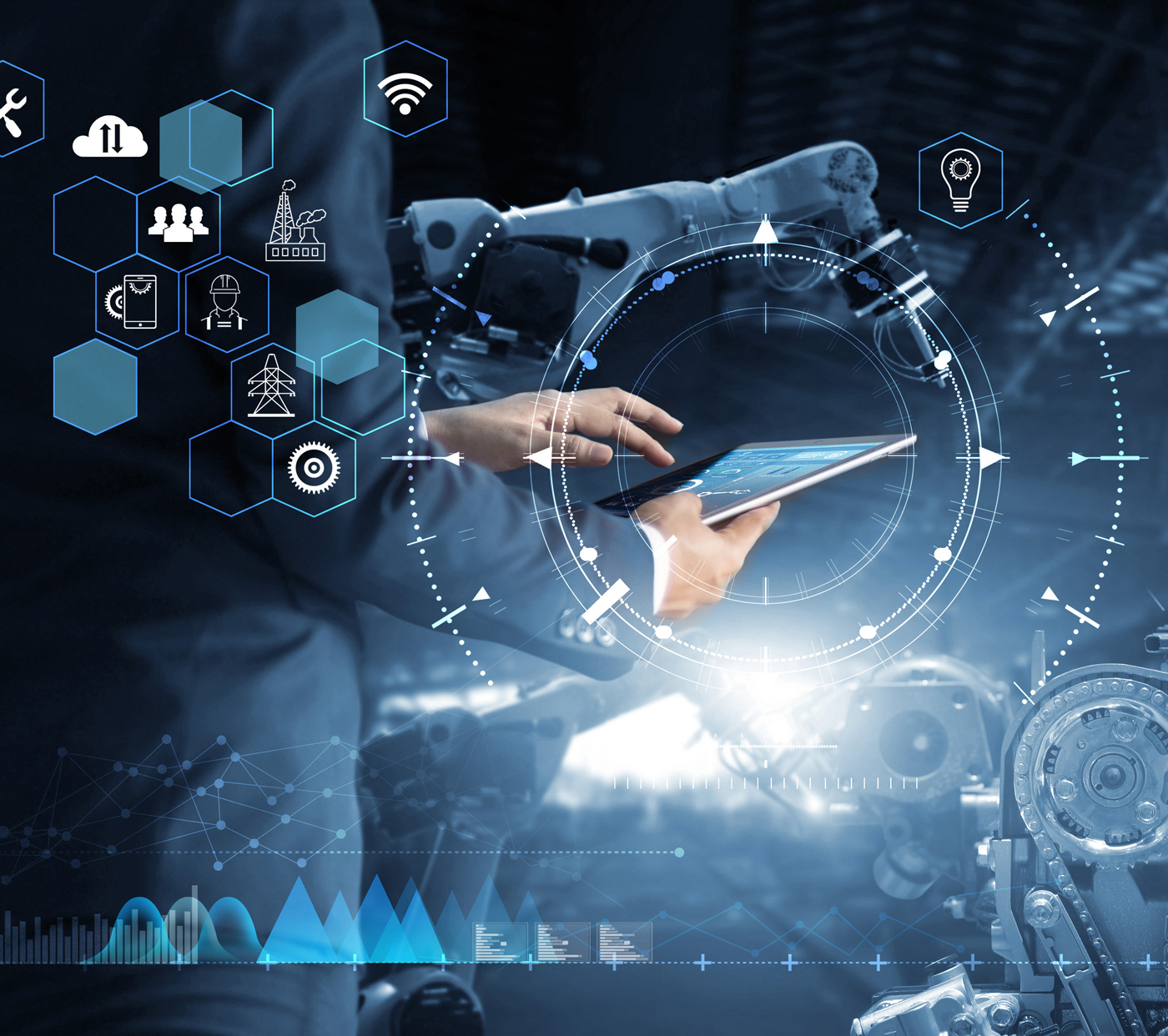
Why the need for a modern EMI?
“The enterprise software layer is not connected consistently to the factory, line, or machine level. Often, data is not collected at all or is fragmented between organizational silos. Manual translation between the enterprise and operations layers (often via a spreadsheet software) leads to limited transparency and is prone to human errors. …. there is a low level of interconnectedness between process steps, few sensors/analytics are built in, and most machines within lines are not interconnected….Despite the progress made by some, very few have achieved a fully integrated industrial automation stack.” — McKinsey & Company, Industry 4.0: Capturing value at scale in discrete manufacturing, July 2019
ThinkIQ delivers a modern and cost-effective alternative to traditional equipment-centric solutions by eliminating information blind-spots that result in risk to revenue.
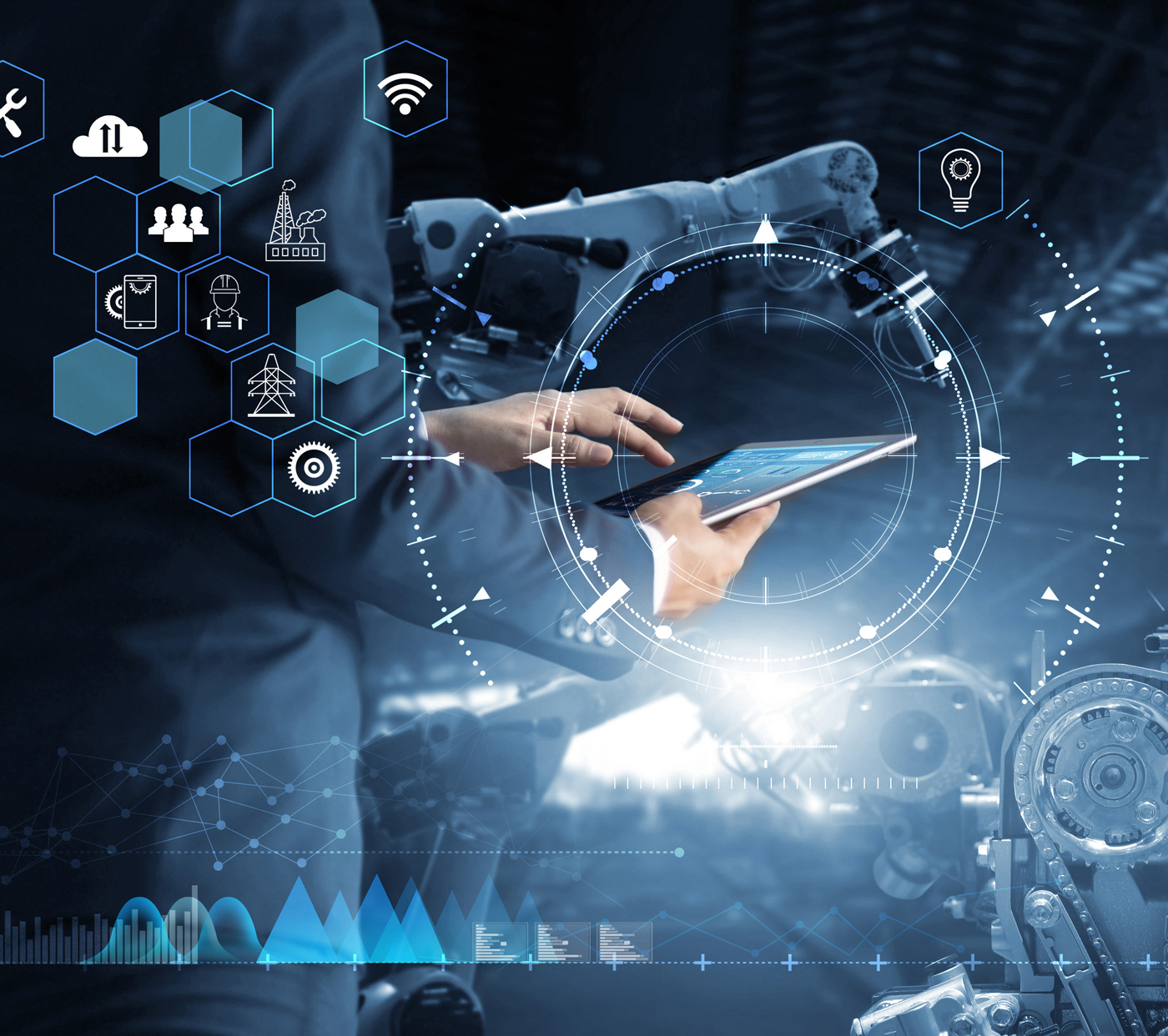
Visibility has been Equipment-centric
ThinkIQ works inside the plant or across the supply chain as a digital twin, bringing material flow and process data together with first principles and modeling to predict potential process problems and provide traceability. Whether you have invested in traditional systems or not, ThinkIQ’s cloud-native and operationally agnostic offering provides manufacturers the unique flexibility to quickly deliver operational insights while also providing a world-class and full-featured platform to support their journey toward Smart Manufacturing.
ThinkIQ works inside the plant or across the supply chain as a digital twin, bringing material flow and process data together with first principles and modeling to predict potential process problems and provide traceability. Whether you have invested in traditional systems or not, ThinkIQ’s cloud-native and operationally agnostic offering provides manufacturers the unique flexibility to quickly deliver operational insights while also providing a world-class and full-featured platform to support their journey toward Smart Manufacturing.
Integrated Operational Controls provide Unparalleled Insight
ThinkIQ also includes the unique ability to collect and organize data compiled from a variety of information sources that affect the manufacturing process. Such source systems include Industrial Internet of Things (IIoT), Manufacturing Execution Systems (MES), Quality Management Systems (QMS), planning and scheduling systems, Enterprise Resource Management (ERP) systems, and others. ThinkIQ connects and unifies these data sources into one accessible analytical model, providing capabilities to explore and drill down into contextualized data based on each end user’s role and point of interest. ThinkIQ recognizes that no two factory or manufacturing operations are the same and as such provides an easy way to collect and harness what is available from location to location.
ThinkIQ also includes the unique ability to collect and organize data compiled from a variety of information sources that affect the manufacturing process. Such source systems include Industrial Internet of Things (IIoT), Manufacturing Execution Systems (MES), Quality Management Systems (QMS), planning and scheduling systems, Enterprise Resource Management (ERP) systems, and others. ThinkIQ connects and unifies these data sources into one accessible analytical model, providing capabilities to explore and drill down into contextualized data based on each end user’s role and point of interest. ThinkIQ recognizes that no two factory or manufacturing operations are the same and as such provides an easy way to collect and harness what is available from location to location.
Features of ThinkIQ for EMI
- Full Data Aggregation
- Real-time and/or historical data reporting
- Enterprise-wide; inside and outside the four walls; capturing data from outside that directly impacts inside the four walls
- Real-time and/or historical data analysis
- Contextualized Data
- Plant-level and/or enterprise-level drill-down analysis
- Advanced analytics
- Comprehensive data visualization
- Scorecards and dashboards
- Custom and standard Key Performance Indicator (KPI) calculations
- Data mining
- Integration and standardization of different data systems/sources
- Full Data Aggregation
- Real-time and/or historical data reporting
- Enterprise-wide; inside and outside the four walls; capturing data from outside that directly impacts inside the four walls
- Real-time and/or historical data analysis
- Contextualized Data
- Plant-level and/or enterprise-level drill-down analysis
- Advanced analytics
- Comprehensive data visualization
- Scorecards and dashboards
- Custom and standard Key Performance Indicator (KPI) calculations
- Data mining
- Integration and standardization of different data systems/sources
Benefits of ThinkIQ for EMI?
Benefits of ThinkIQ for EMI:
- Correlation Analysis – Deep/Contextualized Analytics
- Respond more quickly to changes – Timely Insights & Actionable Intelligence
- Improve overall production performance and manufacturing execution
- Make better, more informed business decisions
- Establish best practices
- Establish benchmarking for continuous improvement
- Support lean initiatives
The rapidly expanding need for just-in-time manufacturing and fulfillment capabilities across industries requires Manufacturing Intelligence systems to play an integral role in driving mission-critical decisions within today’s manufacturing organization.
With ThinkIQ, you can learn what happened, why it happened, predict future events, and then share this intelligence with other systems and workgroups to drive operational efficiency and provide broader decision support impacting issues across your company. Once you have this level of insight, you can confidently take the next step in your journey toward Industry 4.0 Smart Manufacturing.

Contact us today for a no obligation Chemical Supply Chain Traceability demonstration, and to discuss the 5 stages of becoming a Smart Manufacturer.
Faq
What is Enterprise Manufacturing Intelligence (EMI)?
EMI integrates shop floor and enterprise systems for real-time analytics, supporting AI and supply chain decision-making.
How is modern EMI different from traditional EMI?
Modern EMI connects fragmented data sources into manufacturing SaaS platforms to deliver contextualized supply chain management AI.
Why do manufacturers need a modern EMI system?
It improves end-to-end supply chain visibility, eliminates blind spots, and delivers timely insights for smarter decisions.
What systems does ThinkIQ integrate with for EMI?
ThinkIQ supports integration with MES, ERP, QMS, IoT, and more—powering artificial intelligence and supply chain automation.
What are the benefits of ThinkIQ for EMI?
From machine learning and supply chain insights to benchmarking and predictive analytics, ThinkIQ sets the stage for smart manufacturing industry 4.0.