Continuous Intelligence Meets Control Tower
Establishing a Smart Supply Chain Control Tower is easier than you may imagine
Establishing a Smart Supply Chain Control Tower is easier than you may imagine
Frequently Asked Questions On Supply Chain Continuous Intelligence
Manufacturers today are looking for ways to optimize supply chains with contextualized and granular visibility across the entire manufacturing process from a single location. Here are a few of the frequently asked questions you should consider if you are responsible for supply chain optimization, Industry 4.0 or Smart manufacturing initiatives.
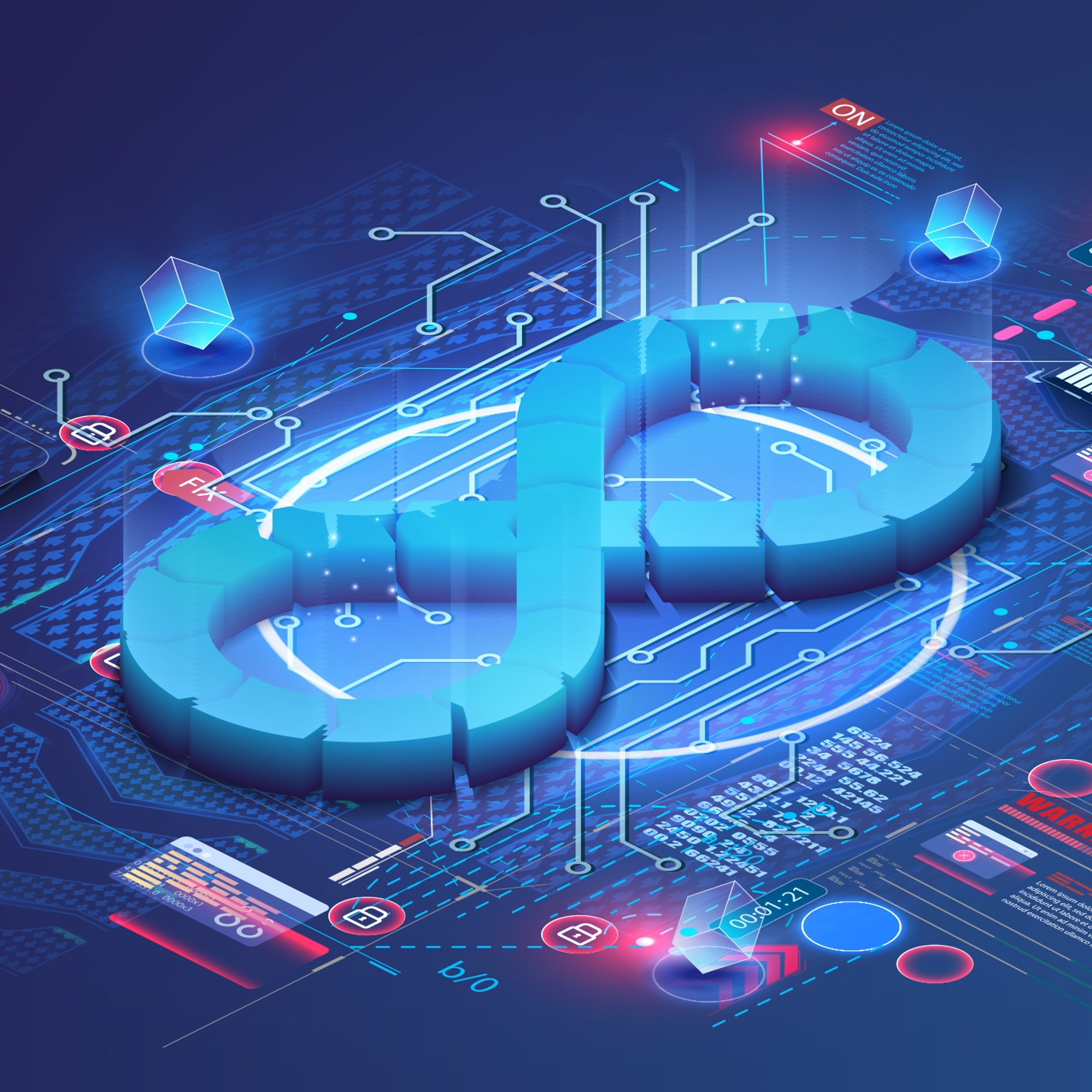
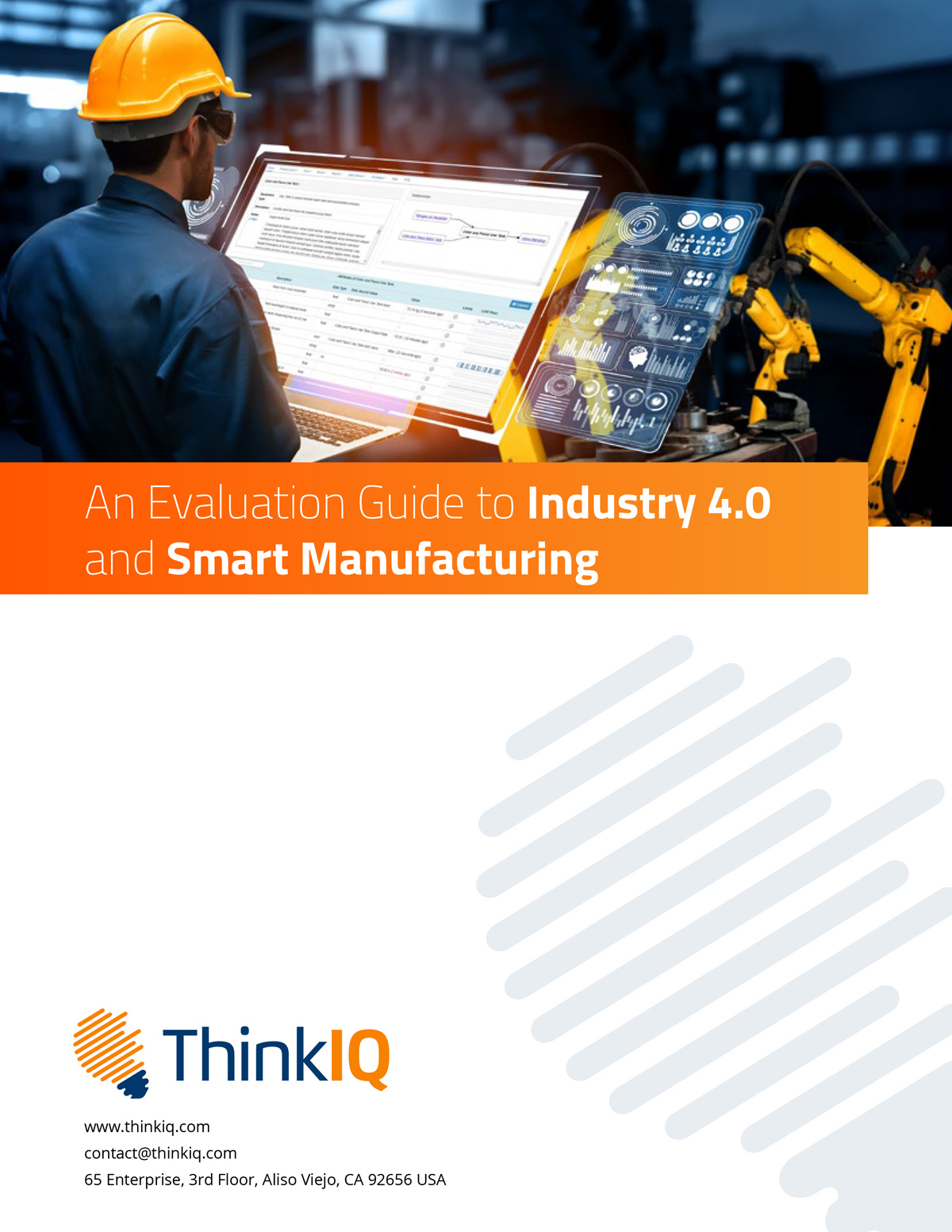
An Evaluation Guide to Industry 4.0 and Smart Manufacturing
Download the eBook which covers the 5 stages needed to fully reach Smart Manufacturing status.
What is a smart supply chain control tower?
Simply put a smart supply chain control tower is a horizontal layer of technology that sits on top of supply chain applications to provide end-to-end visibility and in some cases drive end-to-end process optimization by combining people, process, data, and organization to facilitate smarter decision making.
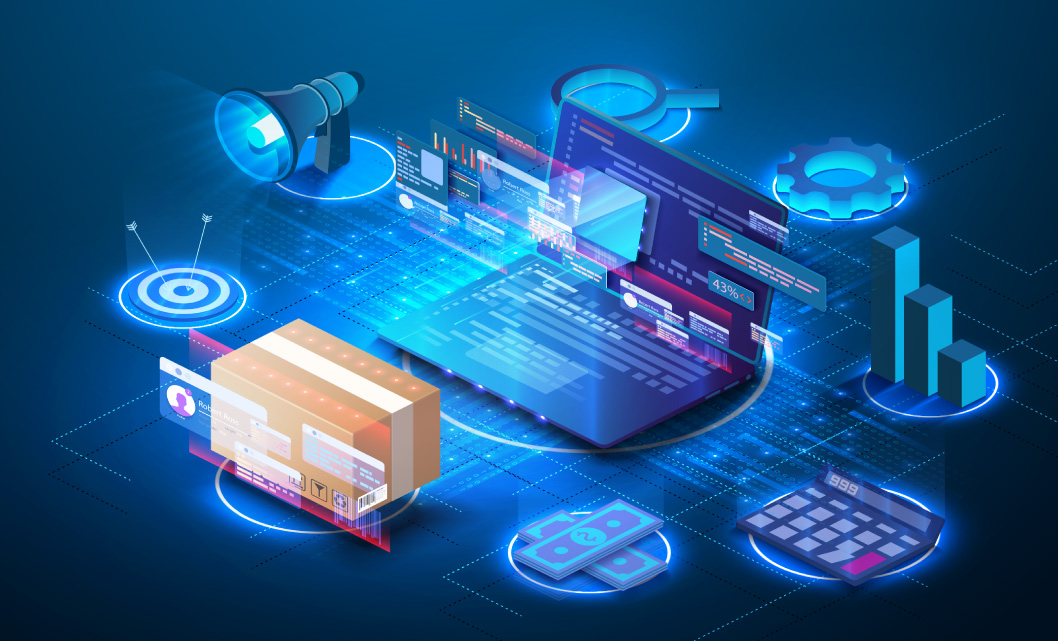
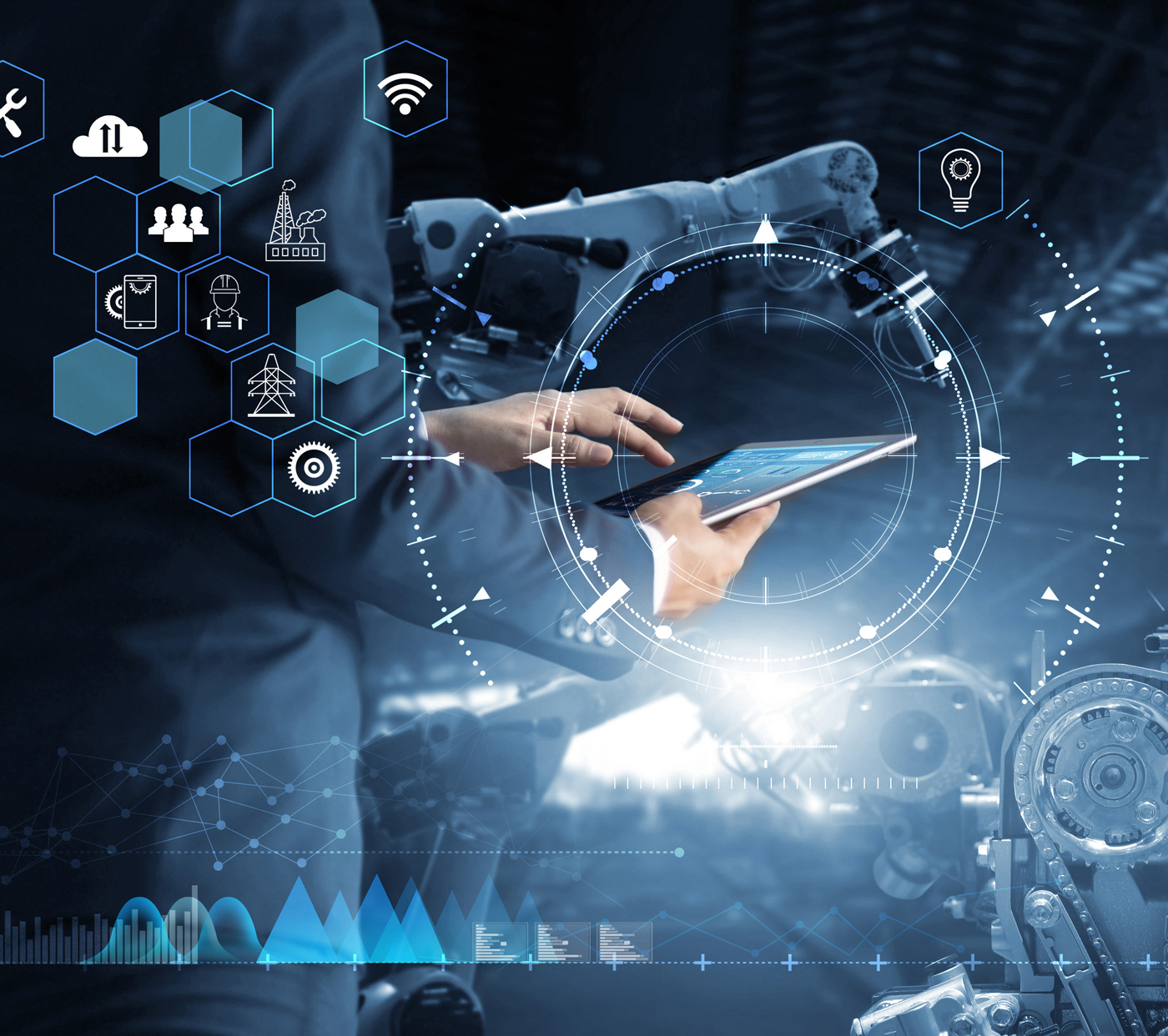
What is the difference between intelligent control towers and traditional distribution management?
Most current supply chain control towers take on a “war room” feel with individuals from across departments throughout the supply chain interrogating spreadsheets or “data swamps” to understand incident responses post-event occurrence. Traditional distribution management approaches oversee the movement of goods from supplier to manufacturer to wholesaler or retailer and finally to the end consumer in roughly the same way. An intelligent control tower automates this process and provides for proactive engagement to prevent potential costly incidents before they happen.
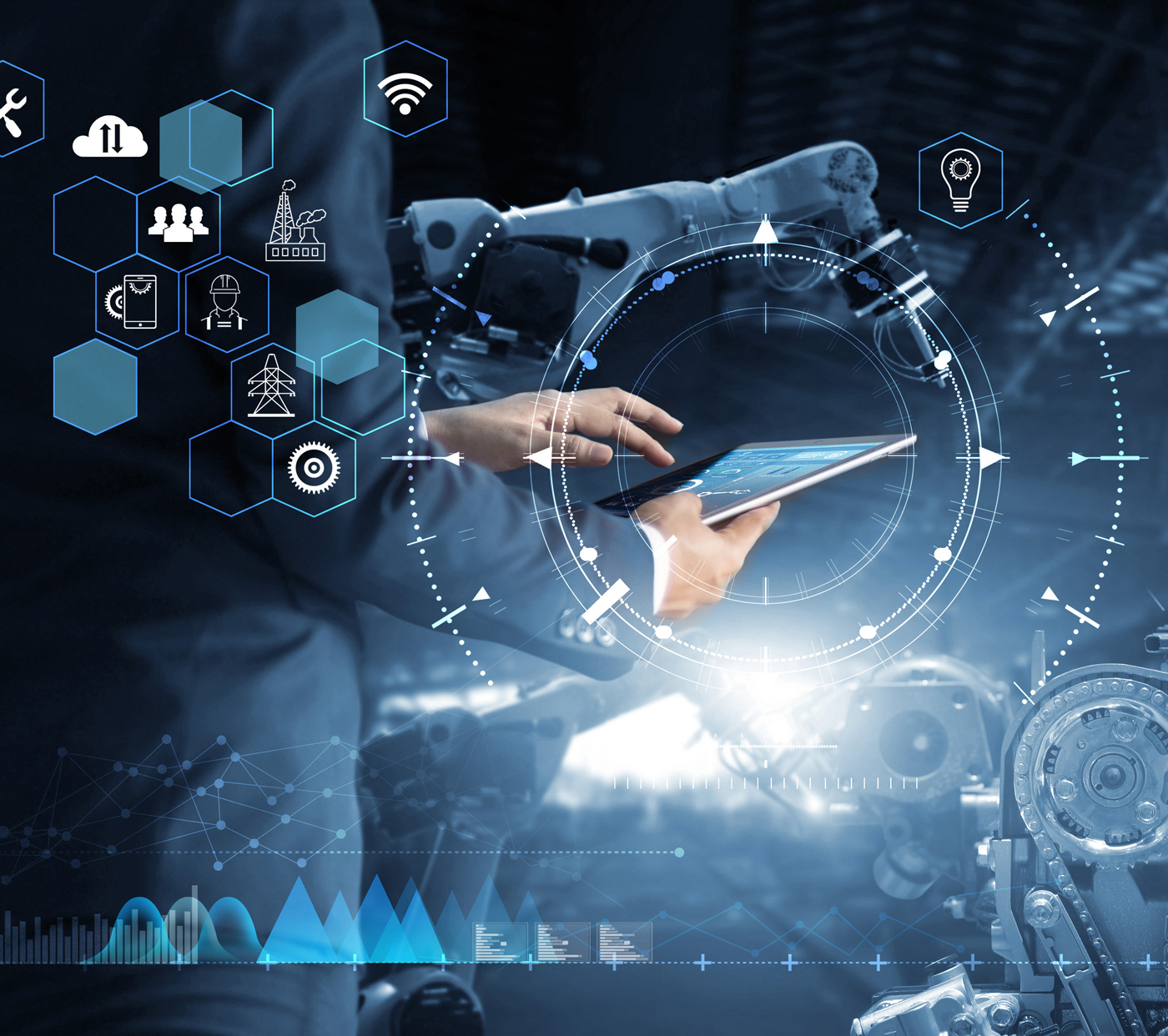
How has machine learning improved control towers?
When you’re dealing with global operations across an entire value chain, siphoning tons of data from internet of things (IoT) sensors and a variety of systems such as ERP, MES, and MOM, the amount of new data you generate is difficult to fully digest and take proper action on. Using Machine Learning and artificial Intelligence to identify material movements, correlations, and root causes will improve yield, quality, safety, and compliance while recalls, waste, and downtime are dramatically minimized.
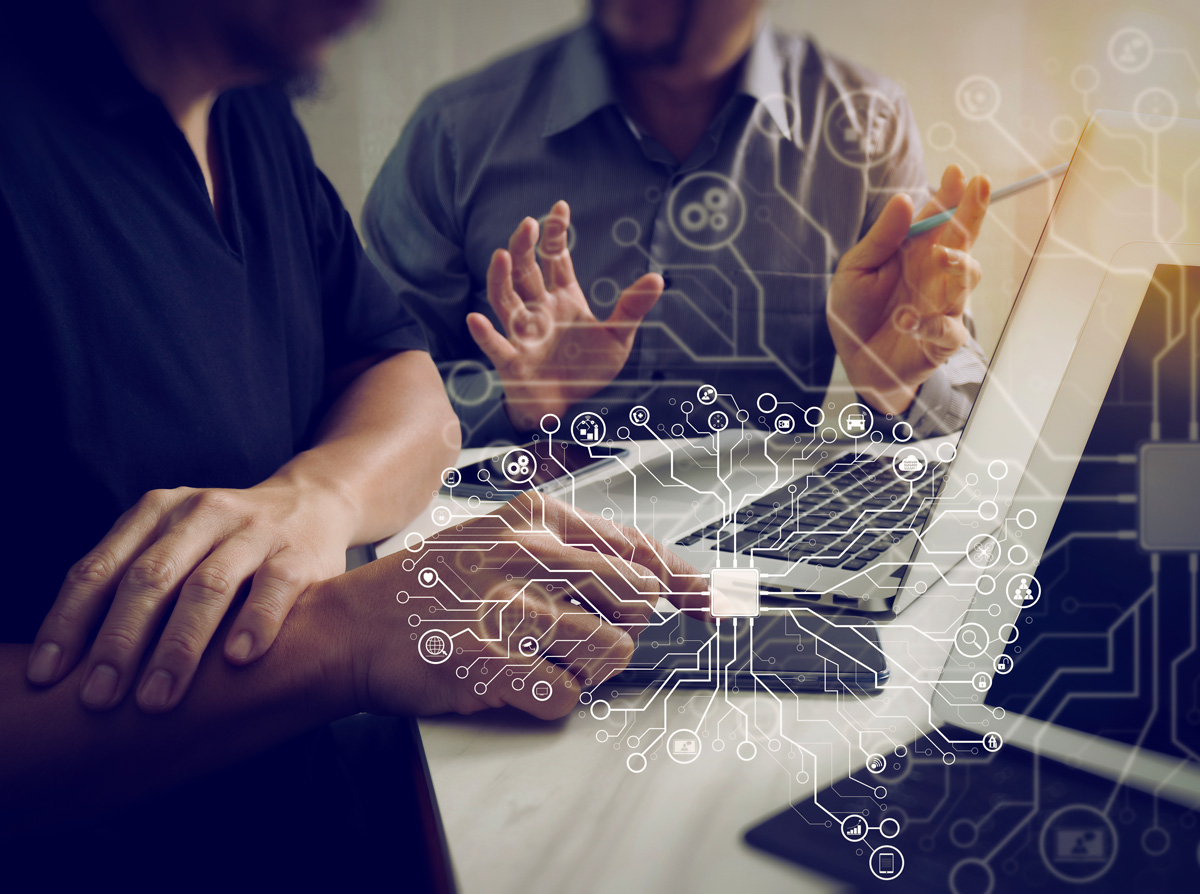
Five benefits of using Continuous intelligence
in a supply chain control tower
Why should you optimize your supply chain using continuous intelligence in a control tower?
By eliminating spreadsheets and manual cross-silo analysis a smart supply chain control tower will significantly speed analysis by reducing analysis paralysis, eliminate manual errors and establish a trusted single source of truth for cross supply chain decision making. A fact-based granular and data-centric contextualized view of material flows and related provenance attribute data provides unprecedented traceability and insight into every single way your operations can improve across the supply chain.
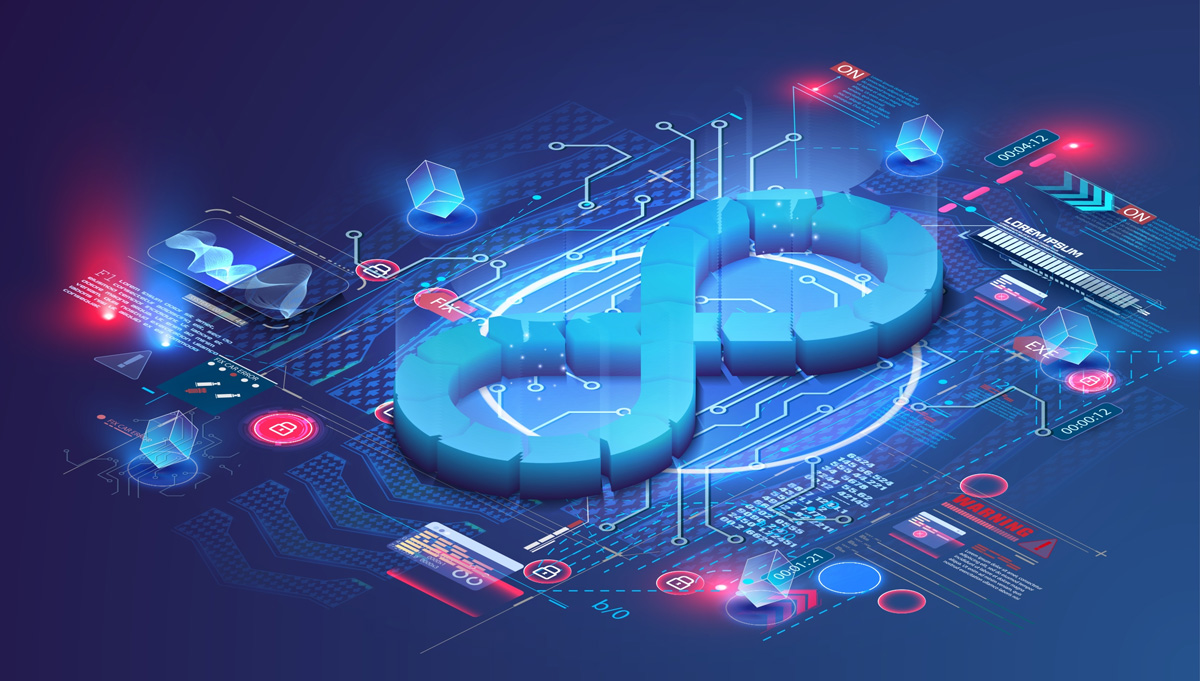
How companies benefit from using continuous intelligence in their control tower?
In the year ahead, traceability comes down to transformational intelligence. By transformational, we mean systems (like a control tower) that proactively reduce the risk of recalls and strengthen safety and compliance, all while maximizing quality, yield, and profit. Enterprise resource planning (ERP), manufacturing execution systems (MES), and manufacturing operations management (MOM) solutions help, but also lack in addressing the entire supply chain and providing proactive, actionable insights through traceability.
What type of data can an intelligent supply chain control tower provide?
Today, most manufacturers, maintain an equipment-centric view of manufacturing operations and if we rely on costly, manual approaches to correlate events with consequences, to quantify material waste, and to know the composition of material at any time, an equipment-centric view is of limited use. The solution lies in material traceability across the supply chain via a control tower. Simply put, the greater visibility a manufacturer can attain of the flow of materials, the greater the yield, quality, safety, compliance, brand confidence, and waste reduction. It’s all part of the movement toward Industry 4.0 smart manufacturing.
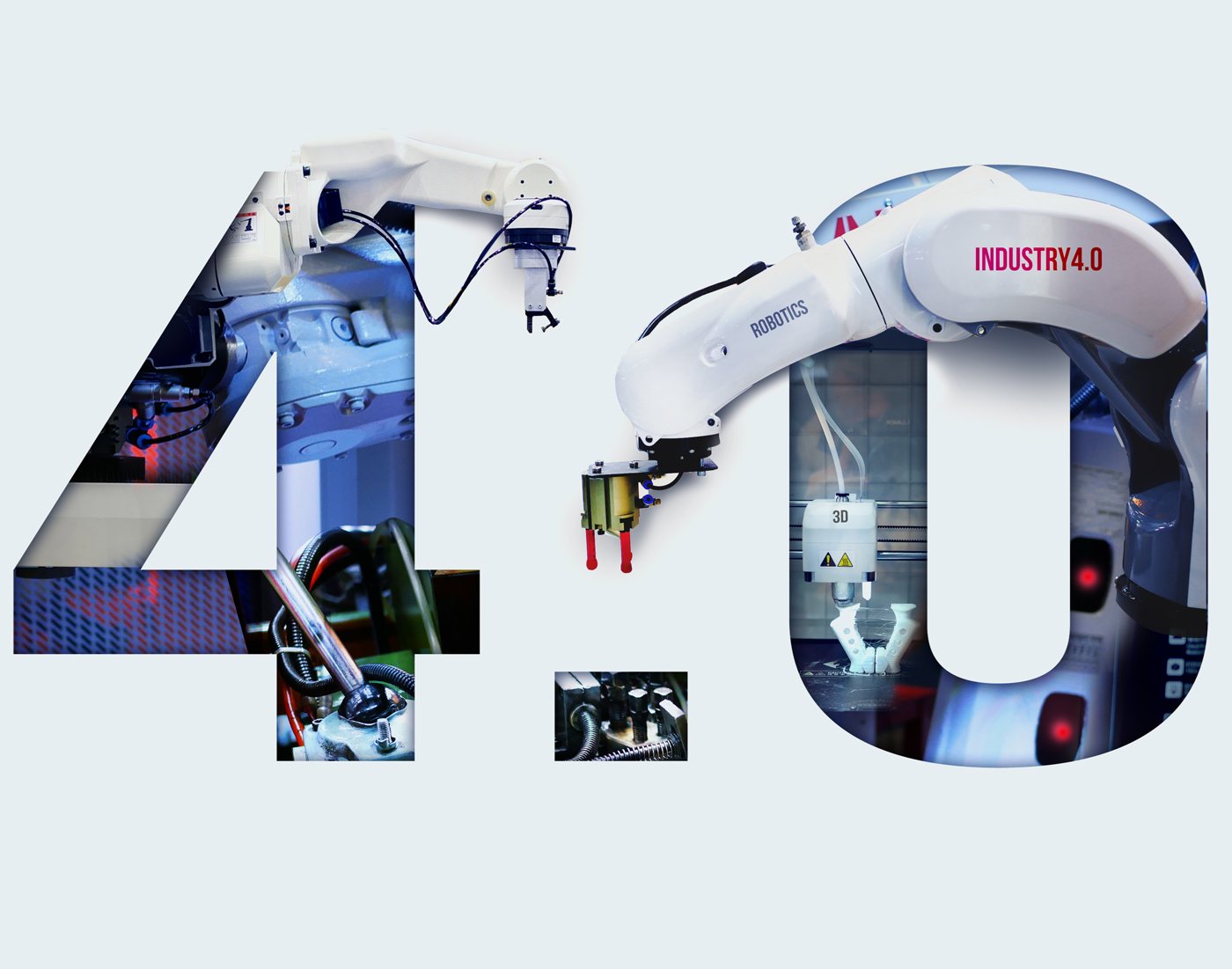
Impact of a smart supply chain control tower on the supply chain
With ThinkIQ’s Smart Manufacturing platform, manufacturers can now develop a smart supply chain control tower for a complete overview of all operations. From raw material to finished good, our smart manufacturing industry 4.0 technology, including our semantic model and material ledger, dramatically reduces recalls, identifies weaknesses in the plant, and eliminates safety concerns.
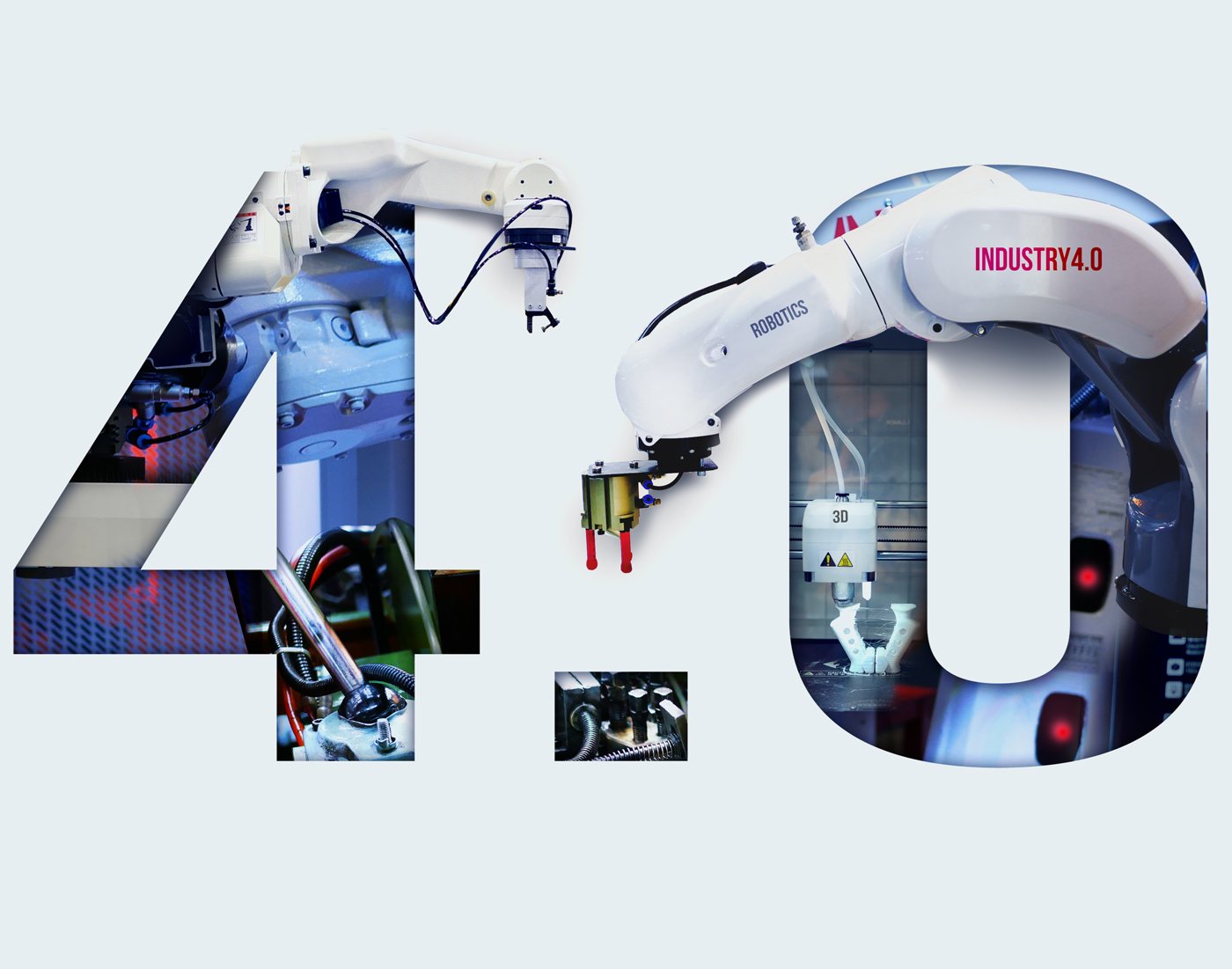
What are the cost savings from implementing a supply chain control tower with continuous intelligence?
While the notion of implementing automated systems for a smart supply chain control tower may sound daunting and expensive, consider that smart manufacturing has accounted for a 25 percent improvement in productivity and a 50 percent reduction in the rate of defects. ThinkIQ continuous intelligence has doubled production yield, eliminated 99.999 percent of recalls, and saved more than $40 million in operational savings for major manufacturers such as General Mills, Mars, and McCain.
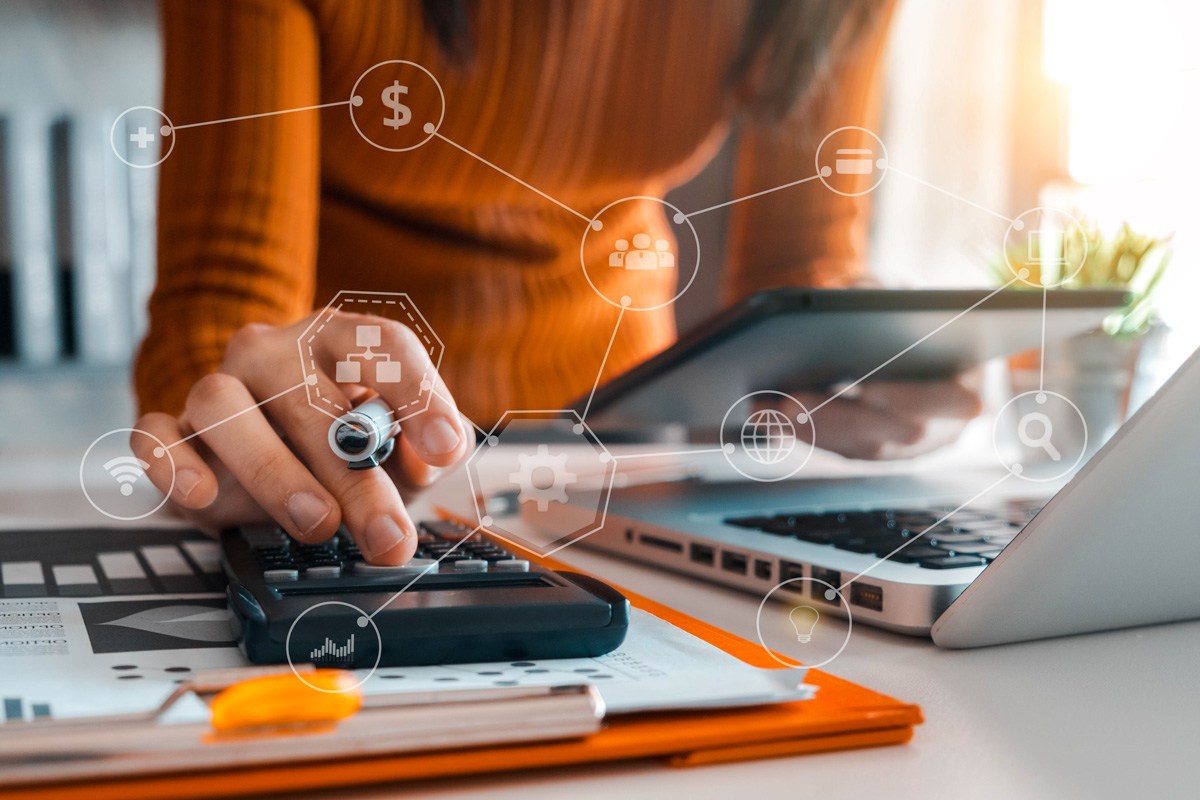
Contact us today for a no obligation Smart Supply Chain Control Tower demonstration, and to discuss the 5 stages of becoming a Smart Manufacturer.
Faq
What is a smart supply chain control tower?
It’s a centralized platform that applies artificial intelligence and supply chain management for real-time, end-to-end visibility and operational control.
How is it different from traditional supply chain management?
It replaces manual, siloed systems with ai supply chain management, enabling proactive decision-making and continuous intelligence.
What are the benefits of continuous intelligence in the supply chain?
Improved traceability, reduced recalls, better safety, and enhanced supply chain and AI integration using predictive analytics.
What data does an intelligent control tower use?
Historians, PLCs, DCSs, IIoT, ERP, MES, QMS and external datasets are unified to enable AI in the supply chain across every touchpoint.
What are the cost savings from using ThinkIQ’s control tower?
Companies report up to 25% productivity gains, 50% fewer defects, and reduced waste—showcasing trends of supply chain management benefits.